Services
For seven decades, DME has been a mold technologies leader. Our catalog remains the industry’s broadest and our products are the benchmark of high quality. Augmenting our superior product line is our expert Service Team which provides our customers with knowledge, expertise, and service that can’t be matched. However, we aren’t satisfied because our customers’ needs keep evolving and we’re determined to help them succeed.
Featuring:
Application Engineering
Hot Runner Service
Controller Repair & Callibration
ProService - CoolingCare
Mold Flow Services
Barrel Repair & Resleeving
Contour Roughing
Project Management
For more information
DME Americas
Engineered Solutions & Services
The DME non-standard mold technologies business requires a more specific approach, one that employs dedicated technical sales specialists supporting customer business requirements through a more project-oriented regimen, especially when compared to the DME standard, catalogue business. DME will serve these special needs customers through a separate non-standard sales organization called “Customized Solutions” (Engineering Solutions Services).
Taking advantage of DME’s global presence, Engineered Solutions & Services works with all DME worldwide locations and best-in-class partners to offer the industry’s widest range of engineered solutions.
The DME Engineered Solutions & Services Group, with comprehensive technical and language skills, offers customers the dedicated project management that utilizes specialized technical support and a cost & delivery-driven focus to provide optimal solutions.
Application Engineering
DME Services
DME’s Applications Engineering Department is focused on one thing – to help you produce better parts. DME customers worldwide utilize our applications engineering expertise for:
- Mold Bases
- Components
- Hot Runner Systems
- Temperature Controls
- Quick-Change Molding Systems
- MRO Products
- Die Sets
- Die Cast Tooling
…and more.
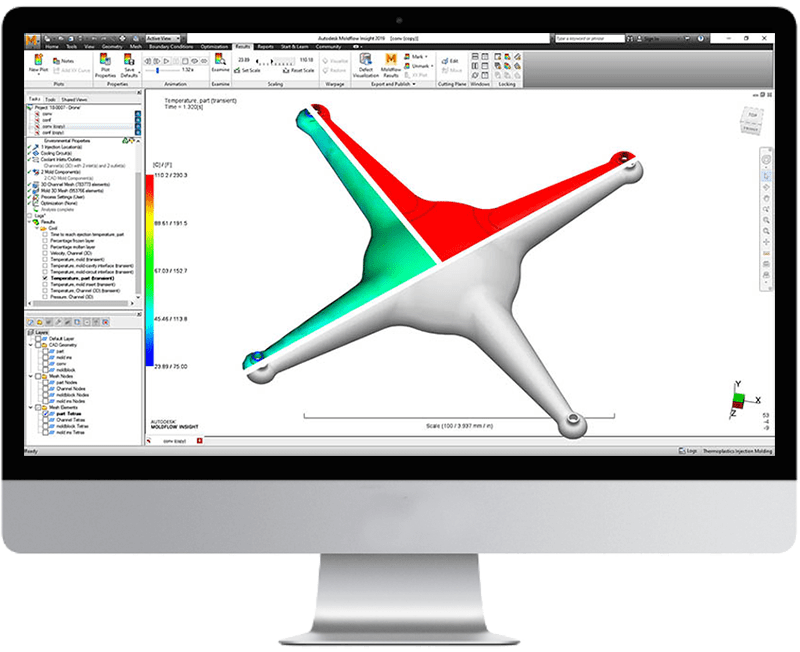
Whether your requirement is a special mold base, a mold action device, a hot runner system or something else, DME Applications Engineering provides solutions that produce optimal results for your specific objective. A keen focus on our customers is a major reason why DME remains the standard-setter in tooling technology against which all others are compared. Contact DME Applications Engineering Services to move forward on your next initiative.
Hot Runner Services & Maintenance
From single nozzles, cool-ones, to fully assembled hot halves … and everything in between
In the relentless drive to reduce costs, improve part quality and speed time to market, hot runners are an increasingly hot item. But every application is unique. How can you ensure you get a hot runner system that delivers all the results you’re looking for in your project? DME is your essential resource for everything in Hot Runners… Every step of the way.
Quick, cost-effective hot runner service
DME is committed to help you optimize the performance of your hot runner systems. Applying the knowledge we’ve gained over nearly 30 years of providing hot runner technology to customers worldwide, the DME hot runner service center continues to deliver fast, cost-effective service. Whether your system is from DME or not, we’ll get it into shape and back in your shop quickly!
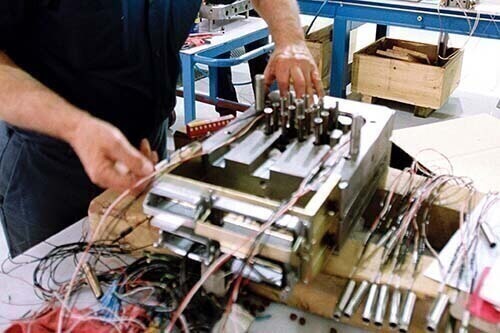
Controller Repair & Calibration
DME understands that every minute your not up and running is money lost, and a poorly functioning controller in unacceptable. DME Controller Service Team is ready to repair your non-functioning controller or calibrate it to required specification. Contact a DME expert today and get back in business.
U.S. Customers:
All TSP, TSP Plus TSP-SVG Systems & TSM modules needing repair or calibration: Please call 800-626-6653 for a Repair SR#, Please make sure this SR# apprears on the outside of the box.
All other temperature controls needing repair or calibration should be sent to:
DME REPAIRS
1419 State Route 45 South
Austinburg, Ohio 44010
Canadian Customers:
All temperature controls needing repair or calibration should be sent to:
DME COMPANY
Unit 3 – 5345 Outer Drive
Oldcastle, Ontario Canada, N9G 0C3
Call 800-387-6600 if you need additional help.
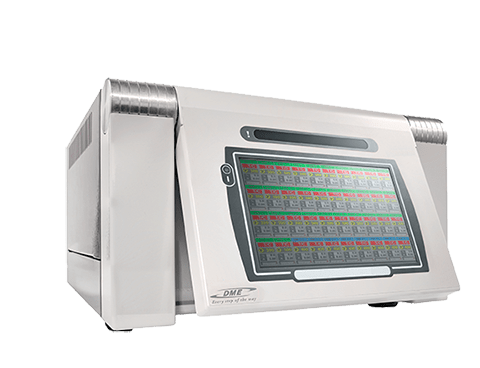
Additional Notes:
Please enclose contact information and a description of what problems you have been experiencing with the product.
Module repairs are a fixed price. Cable and main frame repairs depend on what needs to be serviced. Warranty service is also covered via this method, but module fuses and triacs are not covered.
Contact DME for more information about how we can help restore your control systems so that they they’re working once again at peak performance.
ProService (CoolingCare)
Professional, One Day, Diagnostic & Channel Cleaning Service
DME CoolingCare Pro is an inexpensive, worry free opportunity to experience the benefits of a DME CoolingCare unit in a one day trial.
ProService Benefits Include:
- Clean (1) tool with up to 6 cooling channels in less than 24 hours
- Cleaning media to address various contaminates ($100.00 value)
- On site service technician at no charge ($800.00 value)
- No inventory or storage concerns
- DME coordinated round-trip transportation
- Try-it before you buy-it
- Avoid capital expense approvals
- Service provided in your shop. No need to send the tool out to be cleaned
- Guaranteed improvement of your tool or the service fee is refunded
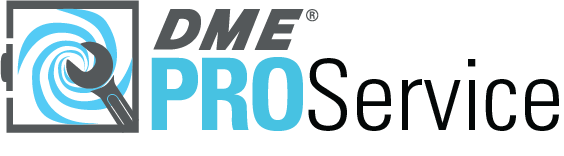
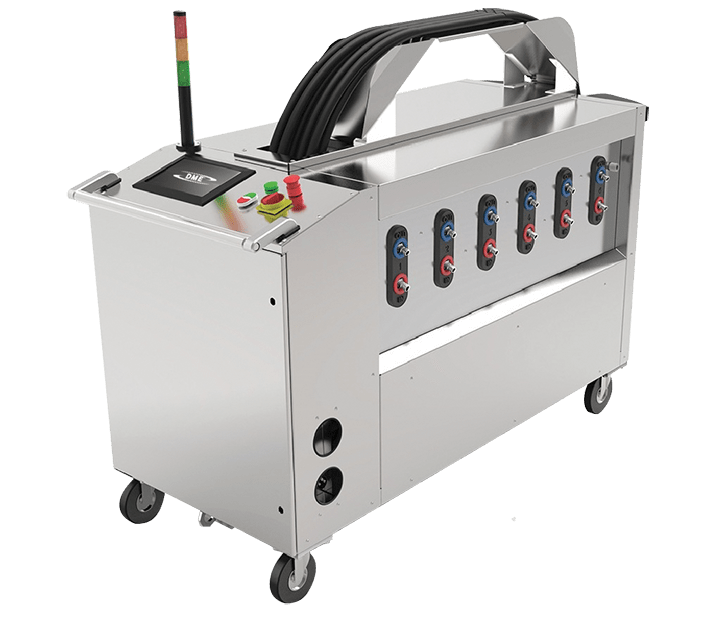
Mold Flow Services
Breaking the Mold with Forward Thinking
A mold design is only as good as it’s functionality. By implementing DME’s analysis services to maximize efficiency of channels and reduce part temperature delta, you can achieve maximum efficiency in your molds with greater return on investment and longer tool life all while producing superior product and reducing waste.
- We understand press operation and capabilities
- Autodesk Moldflow certified staff
- Filling, Packing, Cooling, Warpage, Fiber orientation, Part/Mold
stress and much more - Reduce cycle time and warpage
- Lower scrap and waste
- Increase profit margin
- Enhance mold performance

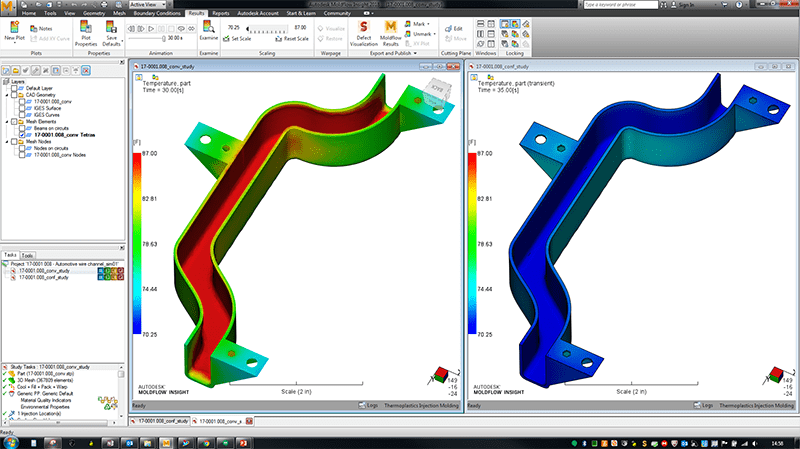
Barrel Repair & Resleeving
DME offers a high-quality low price alternative to competitive barrel resleeving and repair options with fast turnaround time to maximize your uptime. Our service is available for D-2 steel, CPM-10V and CPM-420V.
If your barrel is beyond economical repair, DME stocks new barrels in a wide variety of models and sizes with the highest quality and fastest turnaround time in the industry. Contact DME for more information.
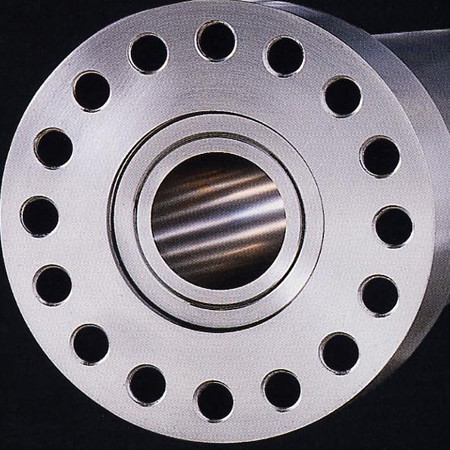
Contour Roughing
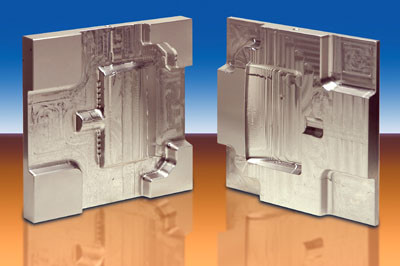
Project Management
DME Project Managers are there to support you when the standard catalogue product just won’t do. Experienced engineers are ready to provide you with the tailored solutions and the custom made parts.
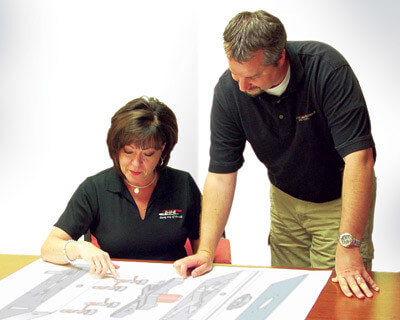
Worldwide:
+1.248.398.6000
USA:
+1.800.626.6653
Canada:
+1.800.387.6600
Mexico:
+52.442.713.5666
Europe:
+32.15.215011
Asia:
+86.775.8601.9031
SUPPORT
Customer Support
Order Support
Documentation
Terms of Sale
Return
FAQ
Services
Hot Runner Service & Repair
ProService (CoolingCare)
Application Engineering
Mold Flow Services
Barrel Repair & Resleeving