CoolingCare
AUTOMATIC CLEANING, DIAGNOSTICS & CONSERVATION OF COOLING CHANNELS – Multiple Functions Allow For Comprehensive Maintenance Of Cooling Channels
Benefits:
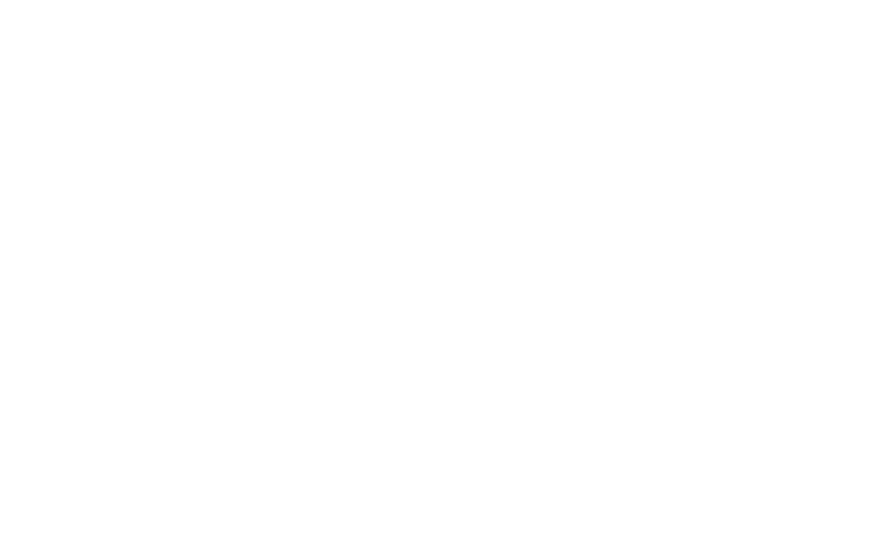
Reduce Maintenance Costs
Clean lines fewer maintenance issues.
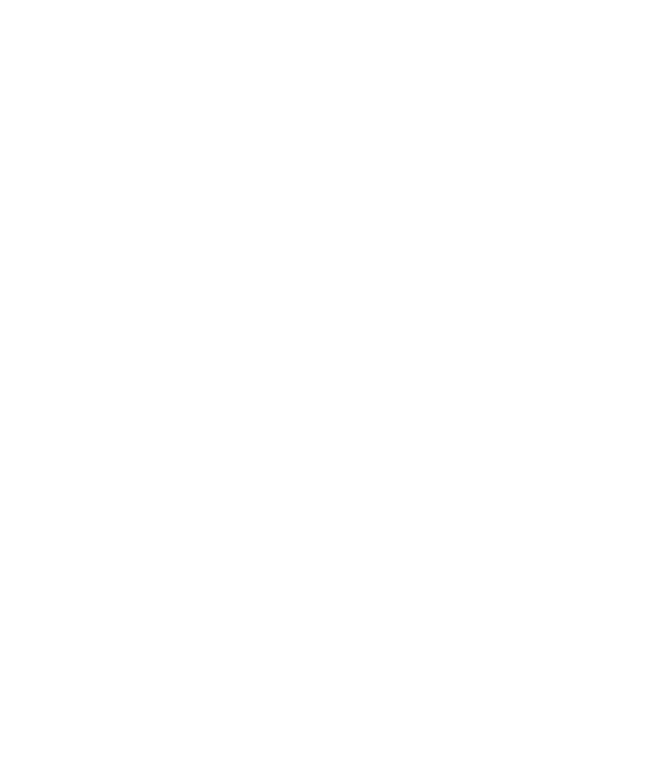
Reduce Cycle Time
Helps maintain proper thermal management culminating in optimized tool performance
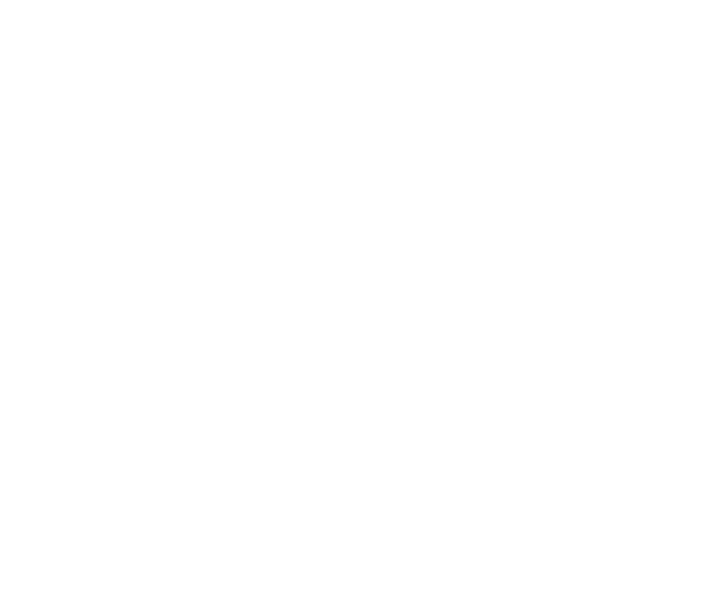
Increase Profit
Optimized tool performance increases throughput – increases profit
Purchase on DME eStore
Exclusive to DME
DME - COOLINGCARE
Overtime cooling channels will become restricted with scale and corrosion build-up. In some cases, the situation can be so bad the entire channels become completely clogged. The result of restricted flow and poor thermal transfer of heat through the water is sub-optimal cooling. This can lead to lower O.E.E. as cycle times become longer and scrap rates increase. Even with operator adjustments the cooling loss cannot be overcome.
The NEW CoolingCare advanced channel cleaning system with Industry 4.0 capabilities is the all-in-one maintenance solution. Patented technology combines a chemical and mechanical action to free and dissolve the unwanted material.
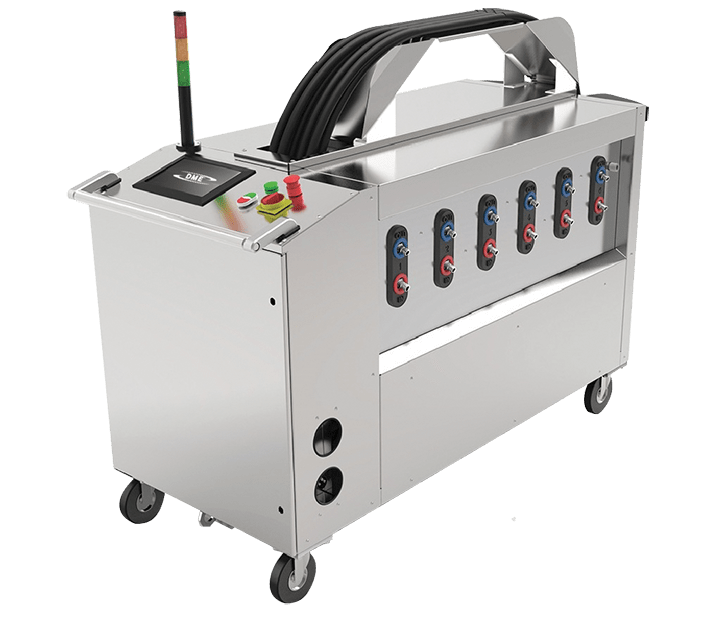
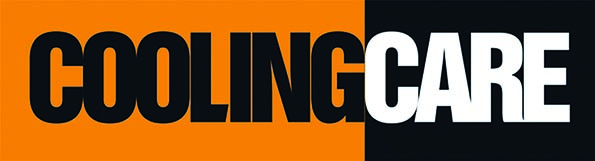
Overview
Multi Function Device – For Comprehensive Cooling Channel Maintenance
DIAMETER (BORE) TEST – Channel leak verification before and after cleaning.
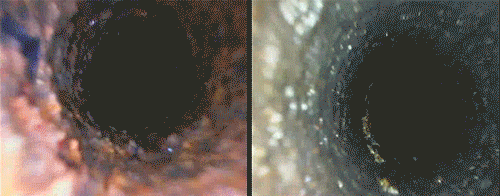
BLOCKAGE TEST – Detection of clogged channels linked to unclogging procedure.
CLEANING – Patent pending channel cleaning process based on two-way pulsating movement of cleaning medium
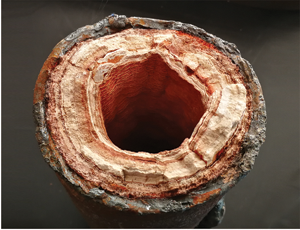
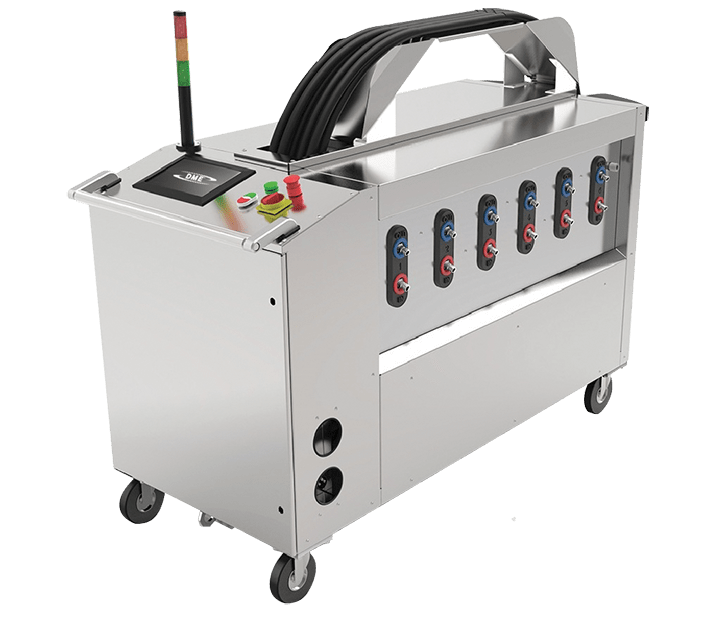
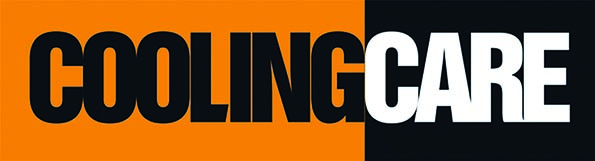
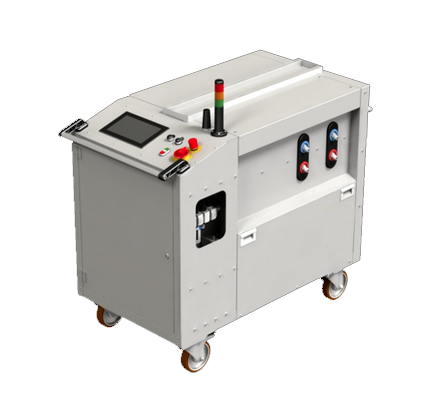
Get THIS Out of Your System!
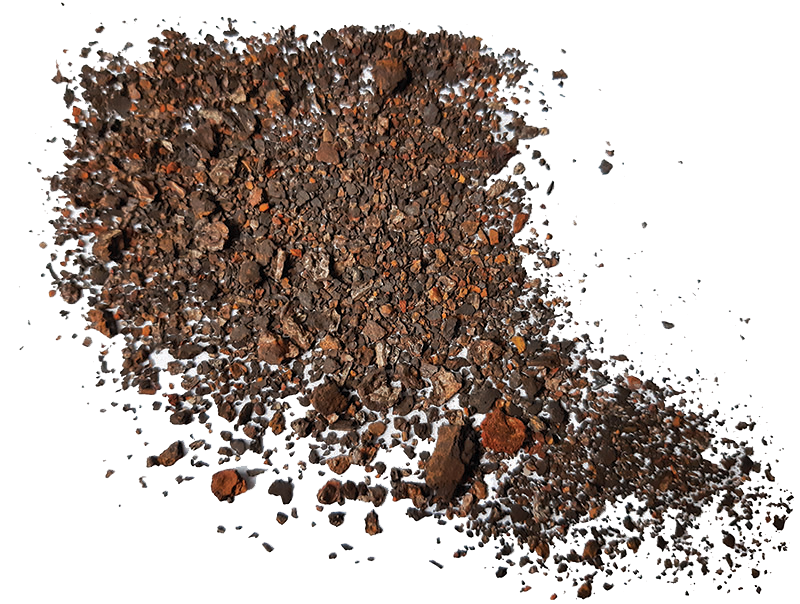
NEUTRALIZATION & CONSERVATION – Protection of channels with corrosion inhibitors at the end of the rinsing process
REPORTING – Record of all process parameters in the database, export of cleaning reports to external devices
DIAGNOSTICS – Flow rate measurement of every channel, comparison of the results with the archived data.
Features
The one-of-a-kind DME CoolingCare mold channel cleaner is optimized for cleaning both conventional and conformal cooled channels.
- User friendly interface
- Fully Automatic – operators are only required to connect the mold and define the channels to be cleaned.
- A unique design allowing for independent and efficient cleaning of channels in most mold applications.
- Advanced archiving system supporting the correct mold maintenance throughout the entire mold operation time.
- High pulsation dynamics of cleaning allows for less aggressive cleaning media-safe for steel, aluminum, copper and bronze.
- Intelligent monitoring of the cleaning process – the device recognizes when the desired flow rate values are reached and finishes cleaning.
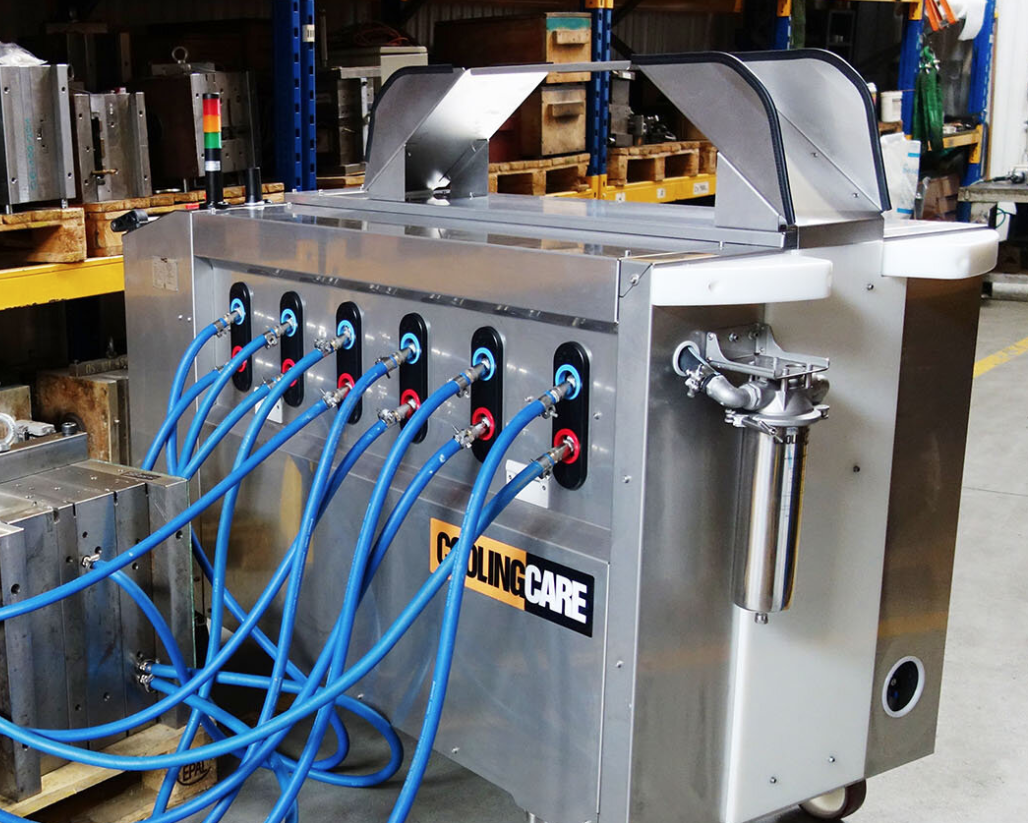
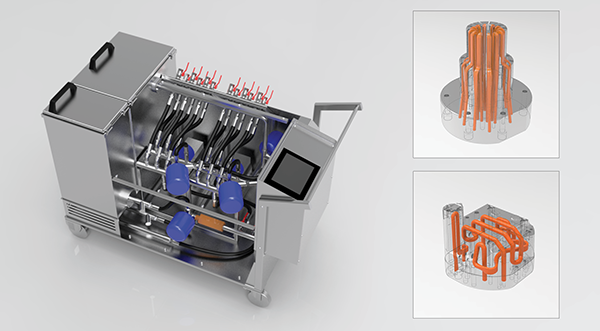
Fully Automated Work Algorithm
Multiple Functions Allow for Comprehensive Maintenance of Cooling Channels
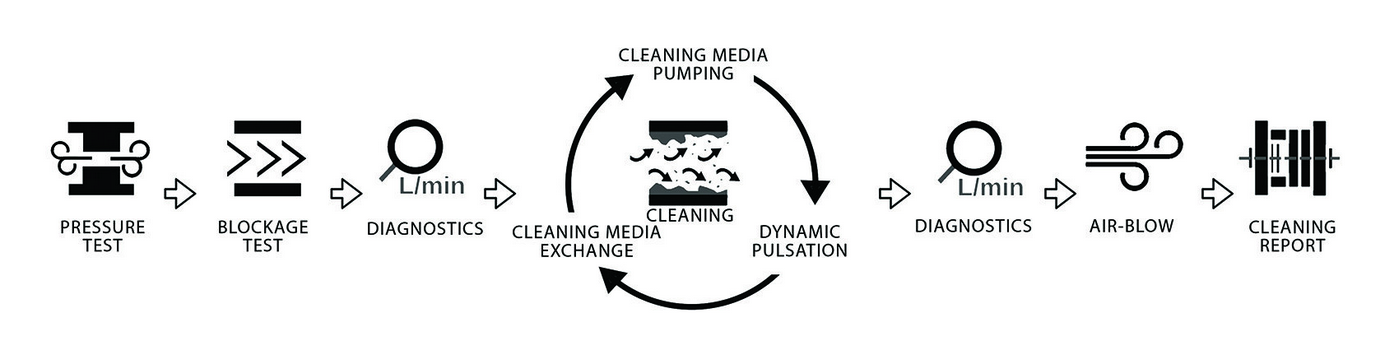
1. PRESSURE/LEAK TEST
Before the machine starts the cleaning process two channel leak verification test are preformed to ensure the cooling channel is air and water tight. The first test is a pneumatic test where the machine will fill the channel with compressed air and will hold for the programmed time and pressure. During this test the machine is analyzing the pressure for any loss which will signify a leak within the channels. If no pressure is lost the machine has confirmed the integrity of the channel and verifies any and all seals are in good working order. If the channel passes the air test the machine will then run the same test with water, again confirming the integrity of the circuit.
2. BLOCKAGE TEST
This test identifies blockages/clogged channels that is not allowing water to flow through the channel. Once the channel is identified as being blocked the machine links to the unclogging procedure to free up the channel. This procedure results in pulsation from both sides of the blockage in a push/pull fashion to quickly free up the channel.
3. DIAGNOSTICS
Flow rates are measurement for each and every channel to set the base line of the current condition. (It is recommend to record all new mold bases the flow rates for each channel prior to running production, this allows the machine to benchmark each tool and clean until the benchmark has been achieve or unit the set time has ran out). A comparison of the results after clean vs with the archived data will be provided in the reporting stage.
4. CLEANING
The CoolingCare unit then starts the channel cleaning process by filling the channels with water based cleaning solution. DME offers two types of media DS1 and DS2, the DS1 has been formulated for cleaning sediment with high concentrations of iron oxides/corrosion by-products while the DS2 is formulated for cleaning scale based on calcium and magnesium carbonates. The machine utilizes heaters to raise the temperature of the cleaning solution to 122F while two-way pulsating pumps move the media in a scrubbing action within channel walls. All of this equates to a highly efficient cleaning process.
5. NEUTRALIZATION & CONSERVATION
Once the cleaning process has been completed the channels are cleared with compressed air. To protection of channels a rinsing process occurs to remove the remaining cleaning solution. Corrosion inhibitors can also be added at the end of the rinsing process to further protect the channels.
6. REPORTING
The PLC is able to record 3,000 tool records of all process parameters within its database. A convenient USB port is mounted on the machine to export cleaning reports to external devices.
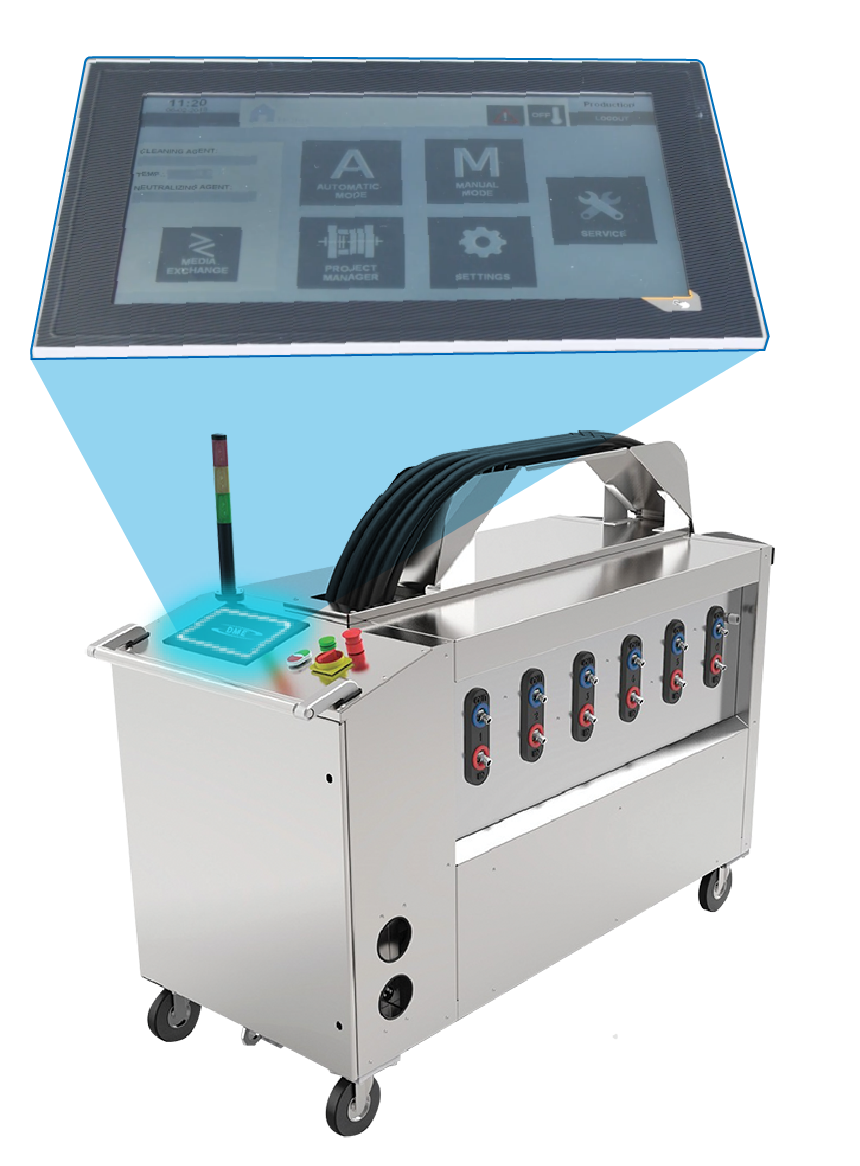
TERMOVISION ANALYSIS of injection molded parts prior to and after channel cleaning
Injection molded parts after cleaning with CoolingCare system show uniform temperature distribution in mold cavities, proving the channels are equally clean. Uniform temperature distribution in all cavities is critical to maintain stable and repeatable process conditions with minimum cycle time and scrap rate.
Regular, preventive cleaning with CoolingCare means stable process conditions and lower mold down-times.
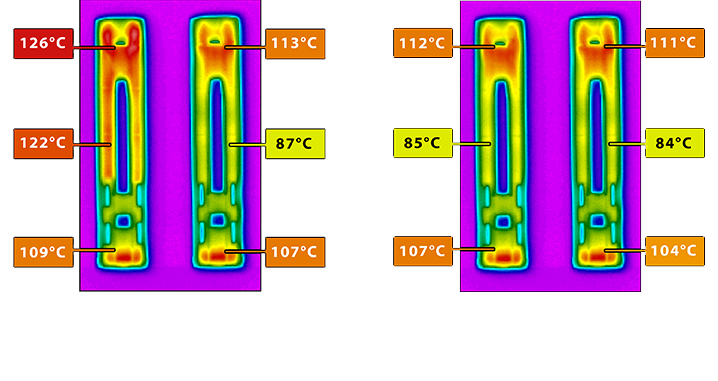
Industry 4.0 Technology
Featuring: Self-Optimization, Intelligent Service and CoolingCare Connect.
CoolingCare features cutting edge functions for comprehensive all-in-one maintenance of cooling channels.
Self-Optimization: An advanced monitoring feature enables the machine to clean until a pre-defined flow rate is obtained or the flow rate becomes consistent. This intelligent feature drives efficiency by adjusting the cleaning cycle accordingly. The ultimate results are maximum cleaning efficiency, and reduced labor costs.
Intelligent Service: uses a built in modem for on-line diagnostics and service. This allows for remote diagnostics of machine malfunction by a service technician. Such a feature reduces and may prevent downtime for machine service related issues.
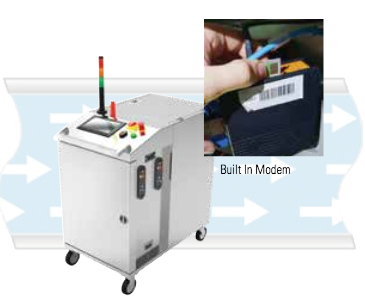
CoolingCare Connect allows an operator to communicate with the machine via text massages. The machine will send a message to the phone of the defined user alerting them of an alarm (up to 17 alarms can be triggered) for unexpected events such as a failed pressure or blockage test, as well as process completion notifications for lights out cleaning.
The operator can also send a test message “S” to the machine requesting its current status. The machine will automatically reply via text message informing the operator of its current mode/action.
This feature requires a GSM card (user provided) to be placed in the modem of the machine for wireless external communications.
The CoolingCare Connect machine’s database allows for the export of cleaning reports to external devices by means of a USB. CoolingCare Connect technology protects your investments, improves profitability, and provides a low maintenance solution to the high maintenance challenges surrounding cooling channels.
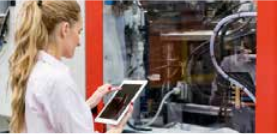
See It In Action
The DME CoolingCare mold cleaning system, was created specifically to maximize the lifespan and efficiency of intricate conformal cooling channels. Its design and implemented functions are the result of practical experience gathered throughout years of designing, manufacturing and using inserts with conformal cooling in injection molding applications.