Hot Runner Services
Time Is Money
When a critical tool is out of commission, productivity is lost and production schedules can be threatened. DME understands this and our technical specialists are always available to get you back in service. Whether you need a total system rebuild, or a simple cleaning and inspection DME can help.
Featuring:
Hot Runner Service
Lifecycle Management
Fluidized Bake Out Service
For more information
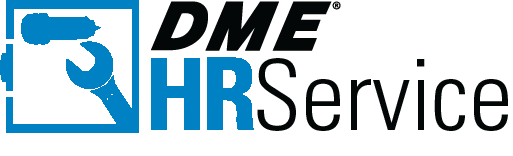
Servicing Your Hot Runners For Over 40 Years
With decades of experience servicing the needs of Molders and Mold Makers, DME is able to leverage it’s unique knowledge base and expert technicians to give customers a robust array of Hot Runner Services and available aftermarket parts.
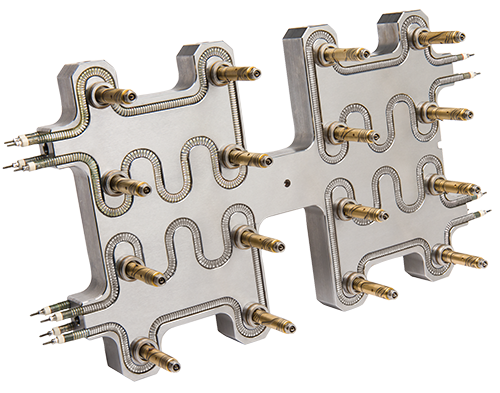
Hot Runner Services & Maintenance
From single nozzles to fully assembled hot halves … and everything in between
In the relentless drive to reduce costs, improve part quality and speed time to market, hot runners are an increasingly hot item. But every application is unique. How can you ensure you get a hot runner system that delivers all the results you’re looking for in your project? DME is your essential resource for everything in Hot Runners… Every step of the way.
Quick, cost-effective hot runner service
DME is committed to help you optimize the performance of your hot runner systems. Applying the knowledge we’ve gained over nearly 30 years of providing hot runner technology to customers worldwide, the DME hot runner service center continues to deliver fast, cost-effective service. Whether your system is from DME or not, we’ll get it into shape and back in your shop quickly!
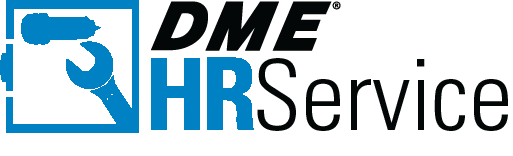
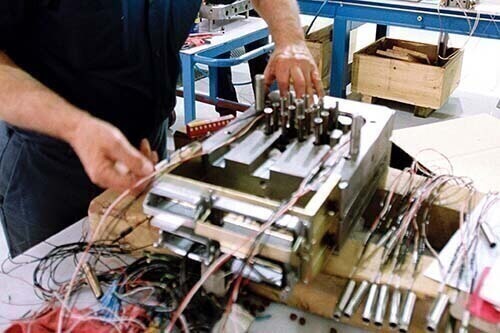
Contact DME Applications Hot Runner Services, by clicking the button below, to move forward on your next initiative.
Maximize Your Productivity
- Complete hot runner system evaluation & diagnostics
- Extended tool lifecycle
- Cleaning and refurbishment of all hot runner systems
- PM programs scheduled for increasing productivity
- Total restoration of flooded systems
- All resins and materials
- Electrical and mechanical validations
- Custom Hot Runner System Evaluations
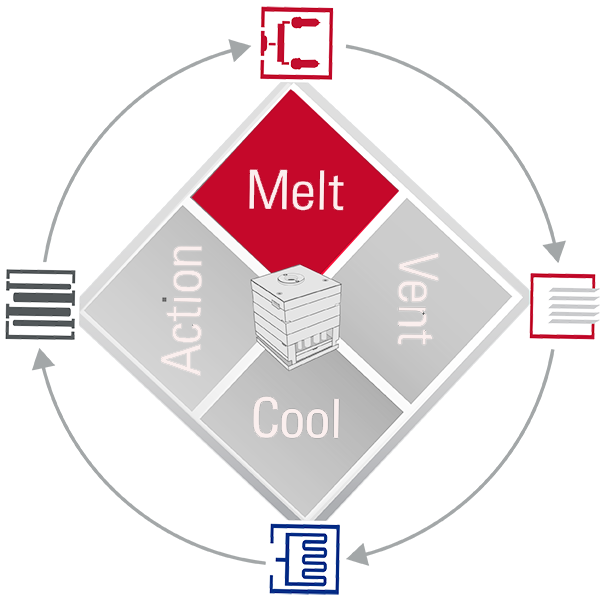
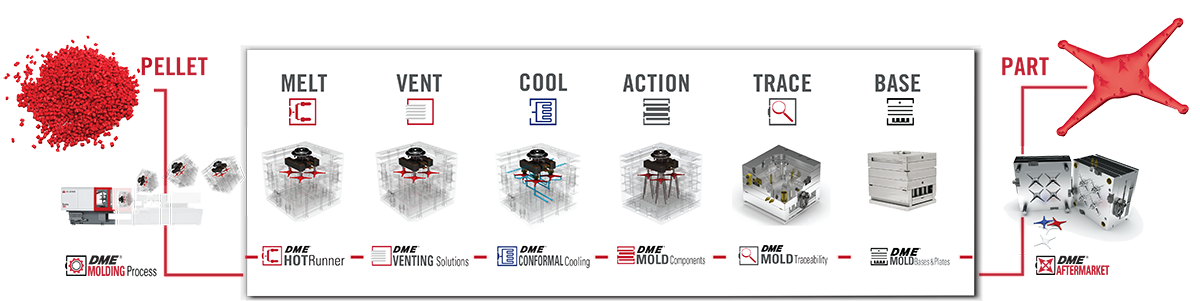
DME Service Centers & Hot Runner Lifecycle Management
Cost-Effective Refurbishments
Cost savings of at least 40% as compared to new systems.
- Extended life of your tool
- Maximizing system uptime and performance.
Whether you need a total system rebuild, or a simple cleaning and inspection DME can help. System rebuilds can be performed on any hot runner system and typically include.

Critical Repairs
Time is money. When a critical tool is out of commission, productivity is lost and production schedules can be threatened. We understand this at DME. That’s why our team of hot runner technical specialists are always available to get you back in service.Whether you’re experiencing leaks, heating issues, flow problems, or would simply like a system bake-out, we’ll repair your system quickly and cost-effectively. Turnaround for system repairs vary due to available replacement parts and work is performed in the order systems are booked. Contact the Hot Runner Service Center for a quote and lead-time on your repair.
Custom Hot Runner System Evaluations
Unable to get parts or repairs via the manufacturer? DME may be able to rebuild new from “manifold to tips” and have you making parts again. Custom manifold and components are made to fit the existing cavity and gate details, maintaining the stackup of the existing system. Heated components are replaced with standard off the shelf DME heated components. Contact the Hot Runner Service center for an Evaluation
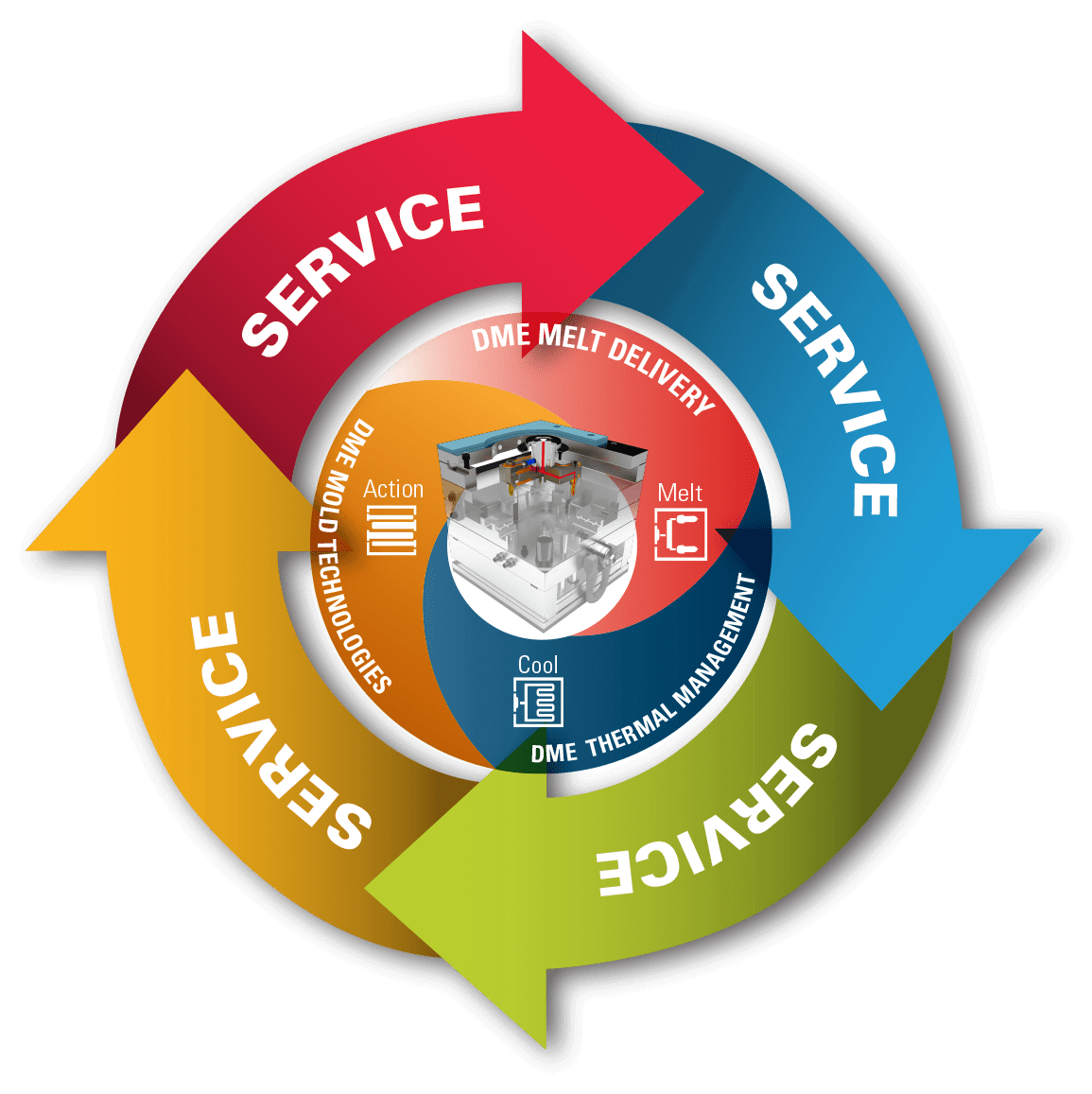
SERVICES OVERVIEW
- Complete bake-out cleaning
- Check and replace heaters and thermocouple
- Inspect and correct wiring
- Replace seals, bushings and other wear items
- Clean or replace nozzle components
- Check and validate all dimensions before re-assembling the system
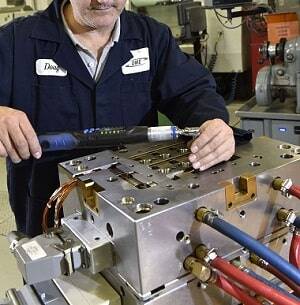
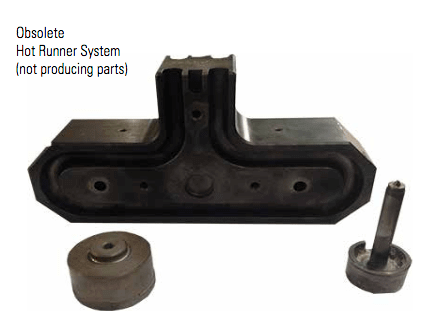
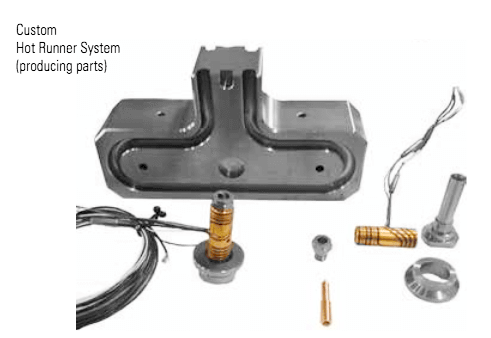
Fluidized Bake Out Service
The fluidized oven scrubs, vaporizes, and burns off all left over resins and carbon material without damaging or warping the work pieces. Once the bake out is complete the cleaned parts are then hoisted out of the oven and set to cool. Now the technicians are able to inspect and evaluate the manifolds specific situation and address any issues.
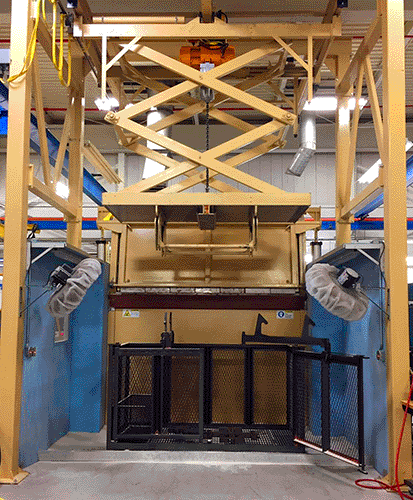